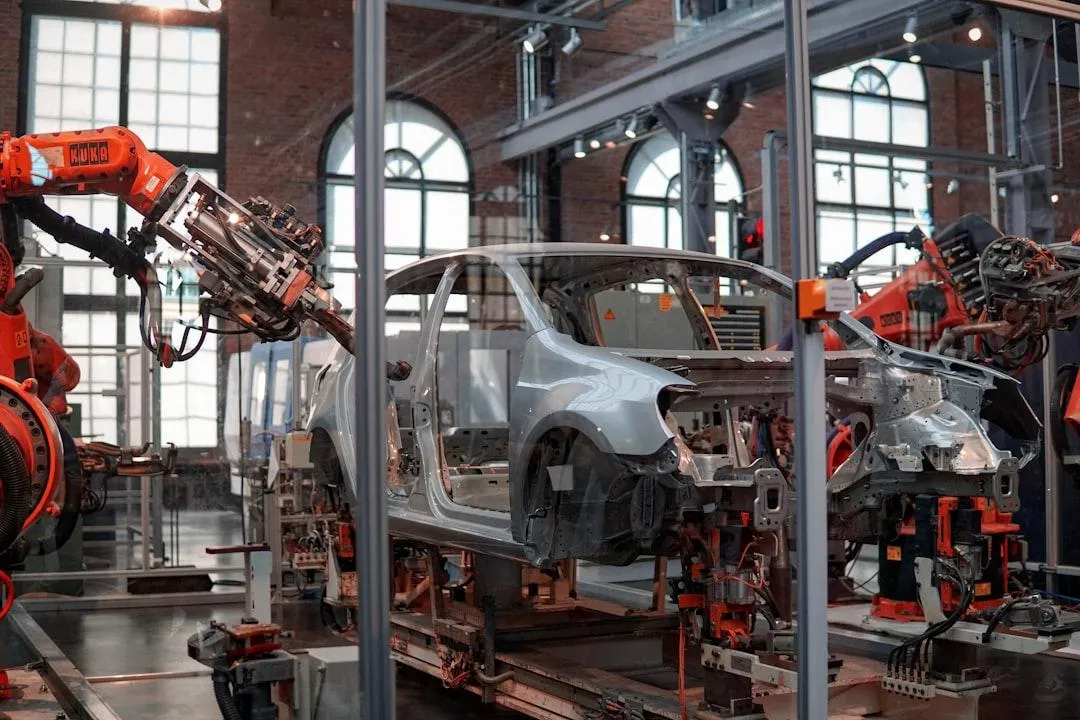
Blue‑Collar, High‑Tech: Closing the IT Vulnerability Gap for Georgia’s Mid‑Sized Manufacturers & Agribusinesses
The Quiet Digital Revolution
Walk into a peanut processing plant in South Georgia or a fabrication shop outside Macon and you’ll find more than conveyor belts and forklifts. You’ll see IoT moisture sensors beaming crop‑quality data to the cloud, precision GPS guiding autonomous sprayers, and robotic welders tied into an ERP system that schedules production down to the minute. These once “blue‑collar” operations now hum with smart tech-and when that tech hiccups, the entire business stutters.
When Machines Stall, Profits Bleed
Across industry studies, unplanned IT or OT (operational technology) downtime costs anywhere from $100,000 to $540,000 per hour for mid‑sized firms, depending on the complexity of the line and margin of the products produced.¹ Manufacturing‑specific research pegs the average at $260,000 per hour, and automotive lines can top $1 million.² Add spoilage for agriculture or lost overtime for crews waiting on a fix, and the math gets painful fast.
Yet, surveys still show many plants treat downtime as an inevitability rather than a solvable risk. Most have recovery playbooks for forklifts or boilers, but not for a failed switch or corrupted VM.
Smart Machines, Soft Underbelly: The Cybersecurity Gap
Georgia Tech’s statewide manufacturing survey found that “nearly all companies are using smart manufacturing technologies, but fewer are paying attention to cybersecurity.”³ In other words, the same sensors and SCADA links that boost yield have quietly widened the attack surface. Rural electric co‑ops, county water systems, and grain elevators have all been hit with ransomware in the past 24 months, often starting with an innocent‑looking phishing email to the front office.
Why the gap?
· Historical under‑investment: Tight margins mean IT has long been viewed as a cost center.
· Blurred ownership: OT teams own the machines; IT owns the network, nobody owns the security glue between them.
· Talent shortage: Cyber pros flock to Atlanta, Charlotte, or Austin, not Cordele or Dublin.
Rural Realities: Why One‑Size‑Fits‑All IT Falls Short
Atlanta‑based MSPs boast impressive SOCs and polished slide decks, but many mid‑state businesses tell the same story: “We’re just another ticket in the queue.” Limited options, long truck‑roll times, and unfamiliarity with niche production systems compound the frustration.
Meanwhile, 22 percent of rural Americans still lack fixed broadband, compared to 1.5 percent of urban residents, hampering cloud migrations and remote support.⁵ When a metro‑centric provider’s canned playbook meets rural constraints, the client ends up paying for services they can’t fully use.
What local owners say they want
1. Fast, plain‑English answers, not tier‑1 scripts.
2. On‑site accountability, the same engineer who designed the network shows up to fix it.
3. Solutions sized for 100+ employees, not Fortune‑500 complexity or pricing.
4. Community commitment, someone who sponsors local organizations and shows up at the Chamber breakfast.
Five First Steps to Future‑Proof Operations
1. Map Your Risk: Inventory every device that touches production, from the tablet on the forklift to the edge router in the grain silo.
2. Baseline Downtime Costs: Multiply throughput per hour by gross margin to quantify true exposure.
3. Segment Networks: Keep office Wi‑Fi, guest Wi‑Fi, and machine networks in separate VLANs with restricted access between them.
4. Patch OT Like IT: Apply vendor firmware updates during scheduled maintenance windows, not “when we remember.”
5. Test the Backup‐and‐Restore Clock: Aim for a full VM restore in <1 hour and a database recovery objective of <15 minutes.
Ready to Close the Gap?
Downtime and data breaches don’t care whether you cut steel or cotton. Let’s keep your lines rolling and your data locked down.
👉 Book a discovery call or reach us at 478‑291‑8620
💯 Take 60 seconds to Check your Cyber Score and see how well you're protected
¹ Atlassian Incident Management KPIs – Cost of Downtime (range $100 K–$540 K per hour).
² Pingdom – Average Cost of Downtime per Industry (manufacturing: $260 K/hour).
³ Georgia Manufacturing Survey 2016 – Georgia Tech Enterprise Innovation Institute.
⁴ HIMSS Analytics – Rural Healthcare IT Connectivity Survey (only 10 % “extremely satisfied” with current network connectivity).
⁵ FCC Broadband Deployment Report 2024 – 22 % of rural Americans lack fixed, terrestrial broadband.